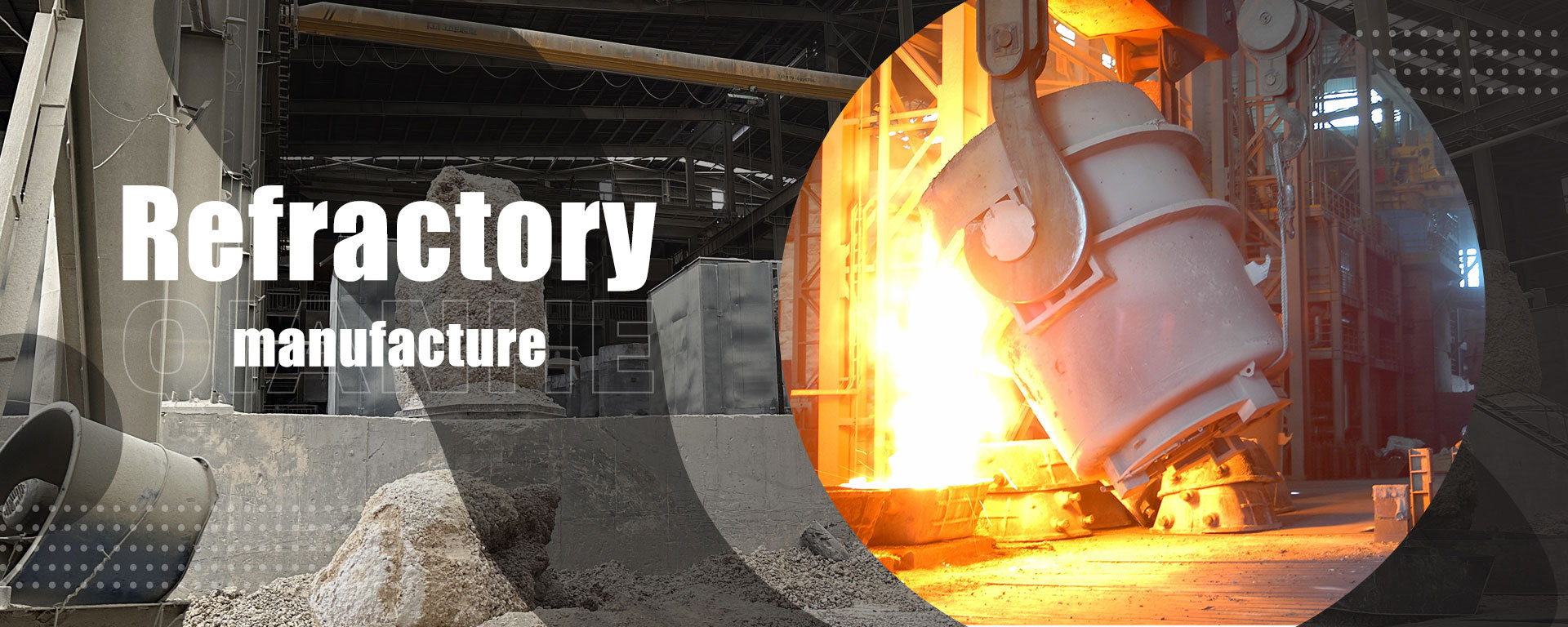
Notes d'utilisation de la magnésie de qualité moyenne : 98 magnésie fondue
2024-01-10 09:04Notes d'utilisation de la magnésie de qualité moyenne : 98 magnésie fondue
Résistance à l'oxydation : les réfractaires ont une bonne résistance aux chocs thermiques et aux scories car ils contiennent du carbone, mais leur inconvénient est une oxydation facile. Une fois le carbone oxydé, ses avantages disparaissent. Pour démontrer pleinement les avantages des réfractaires à base de magnésie de milieu de gamme, des additifs appropriés sont souvent ajoutés pour améliorer leur résistance à l'oxydation. En raison de sa bonne activité, facile à réagir avec l'oxygène, le cobalt, l'aluminium, le silicium, le magnésium et d'autres éléments, le métal est utilisé comme antioxydant des matériaux réfractaires et son alliage est couramment utilisé comme antioxydant.
Réaction in situ pour produire du non-oxyde : le métal est introduit dans le réfractaire et le métal réagit avec la composition du matériau ou le gaz environnant pendant le processus de combustion pour former une phase de renforcement et de trempe non métallique, ce qui améliore la matrice dans la pièce. résistance à la température, aux températures élevées et aux chocs thermiques. Aujourd’hui, cette compétence est largement mise en avant.
Marché de la magnésie fondue électrique
On peut voir que l'ajout de métal dans l'estimation des réfractaires à base de magnésie de qualité moyenne a un effet frappant sur les propriétés mécaniques et la résistance à l'oxydation des réfractaires, ce qui indique que la magnésie de qualité moyenne a de larges perspectives d'application dans l'estimation des réfractaires. . En raison du développement continu de la science et de la percée continue de la portée scientifique, la fonction des matériaux réfractaires sera continuellement optimisée et son échelle d'application sera encore élargie.
1. Moulage : fait de tôle d'acier ou de bois dur, agent de finition de tôle d'acier (huile), peinture imperméable sur le panneau, ne doit pas fuir de pulpe et a une bonne résistance.
2. Agitation : Remuez avec un équipement professionnel, mettez d'abord le matériau dans l'équipement, retirez les additifs, mélangez à sec pendant 2 à 3 minutes, puis ajoutez de l'eau pour remuer pendant 3 à 5 minutes, ajoutez de l'eau appropriée.
3. Compactage par vibration : Versez le béton coulé dans le moule, immédiatement le compactage, ne doit pas fuir dans une certaine direction, ne doit pas être dans la même direction de compactage, afin d'empêcher la ségrégation et l'ouverture du béton. Le béton doit être mélangé hors de l'eau dans les 20 à 30 minutes et le condensat primaire doit être jeté.
4. Protection : l'apparence du coulable est terne, la résistance atteint 70 % et le moule peut être retiré pendant 24 heures et 48 heures.
5. Four : Selon l'épaisseur des différentes marques et bétons et leurs conditions climatiques, les utilisateurs doivent garantir 72 heures de temps de cuisson.